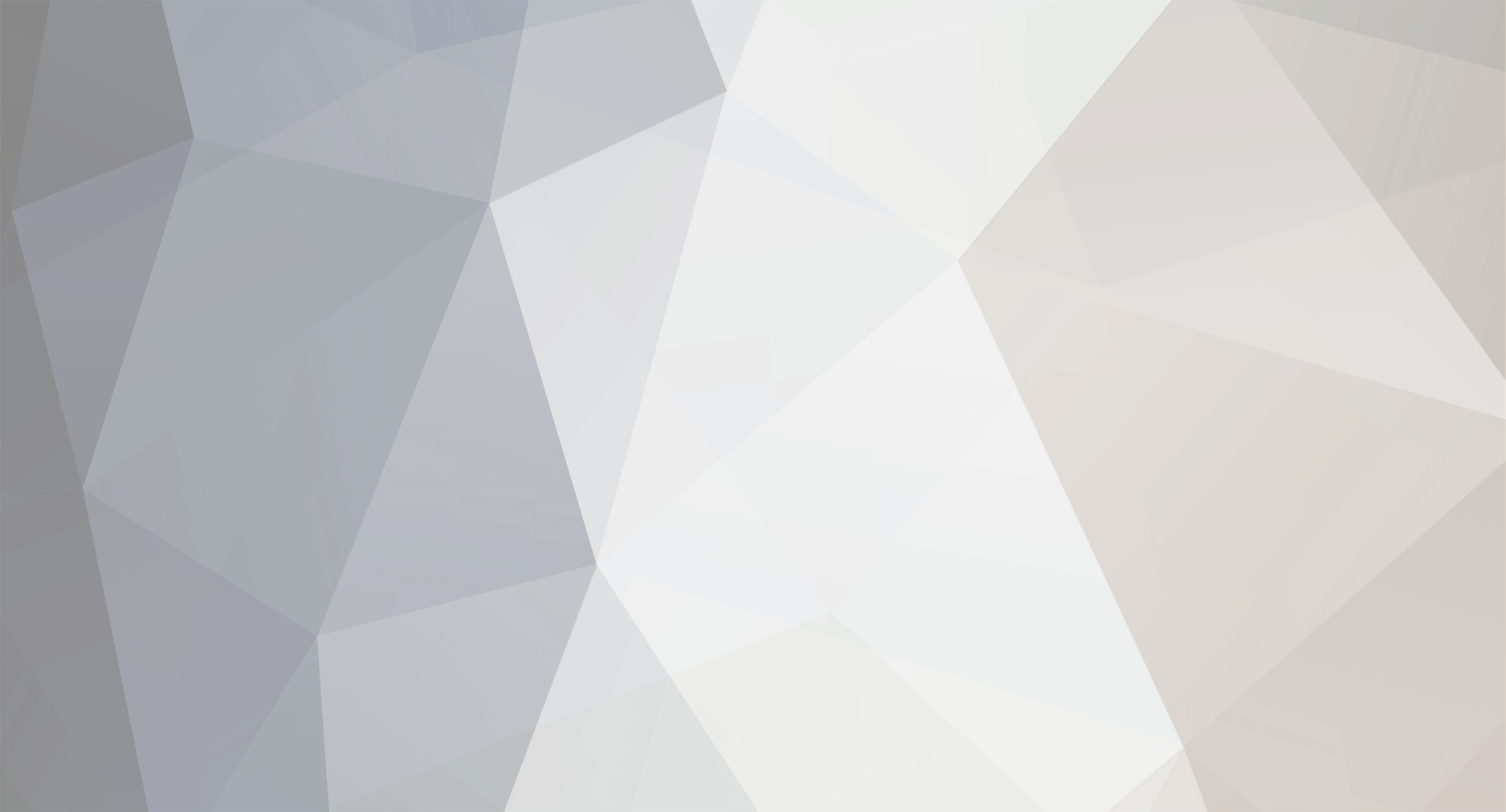
Vicaeman
Membres-
Compteur de contenus
43 -
Inscrit(e) le
-
Dernière visite
Récompenses de Vicaeman
-
Etude pour fabriquer une imprimante 3D à commercialiser
Vicaeman en réponse au topic de Vicaeman dans Projets et impressions 3D
Aha nan la JBL n'est pas vendue, elle sert à maintenir le plateau car l'axe est tellement clean au niveau du contact tube en carbone/roulement à bille que ça descend tout seul. D'ailleurs les tubes en carbones font 2mm d'épaisseur (c'est du 10mm diamètre extérieur et 6 mm intérieur : https://www.tubecarbone.com/fr/tubes-carbone-int-0-a-10mm/1078-tube-carbone-06x10mm-drapage-rectification.html)je me suis dit que c'était intéressant pour alléger plutôt que prendre des arbres pleins en acier. Le seul inconvénient en effet c'est le coût. Mais je tente ce compromis, je verrai à l'utilisation si ça en vaut vraiment la peine. Pour le réglage du plateau les molettes c'est plus du "design" car j'utilise le capteur piezo de chez piezo orion (https://www.precisionpiezo.co.uk/product-page/precision-piezo-orion-kit) pour avoir un auto bed leveling. Le réglage des molettes se fera donc une seule fois lors du montage. Pour les équerres je souhaitais quelque chose de discret pour la fixation. En réalité la structure bouge pas d'un poil car chaque profilé est maintenu par 4 de ces équerres. Après si tu vois un autre type de fixation qui serait peut-être plus qualitatif je suis preneur. J'ai aussi 2 tubes pour maintenir le x tout en allégeant, c'est plus utile dans cette condition.- 65 réponses
-
- imprimante 3d
- projet
-
(et 1 en plus)
Étiqueté avec :
-
Etude pour fabriquer une imprimante 3D à commercialiser
Vicaeman en réponse au topic de Vicaeman dans Projets et impressions 3D
Salut @divers . En effet sur le modèle visible ici j'étais parti sur un système de plateau mobile mais qui prenait beaucoup de place donc oui la course en était vraiment pas élevée. Mais depuis l'imprimante a bien changé. Le projet avance toujours, d'ailleurs j'ai pratiquement terminé il me reste un peu d'assemblage à faire. Je ferai une mise à jour très bientôt. Côté création de l'entreprise c'est en stand by temporairement. Je poste un petit aperçu ici de l'avancée.- 65 réponses
-
- 3
-
-
- imprimante 3d
- projet
-
(et 1 en plus)
Étiqueté avec :
-
Etude pour fabriquer une imprimante 3D à commercialiser
Vicaeman en réponse au topic de Vicaeman dans Projets et impressions 3D
Salut @divers, j'y travaille encore. Ces derniers temps j'ai plus travaillé sur la partie "Business plan" pour la vente que l'imprimante elle-même. J'ai du présenter le projet devant des experts (marketing, comptable, banquier, juridique etc.) pour connaître la viabilité. Je mène aussi une étude de marché en parallèle et mes études.. du coup c'est compliqué de combiner tout ça mais ça avance quand même. L'objectif fixé est de sortir un prototype final d'ici le 24 Mai si tout se passe bien. Voilà pour les nouvelles. Merci de continuer à porter un intérêt à ce projet, ça me motive d'autant plus Un petit aperçu rapide de la conception en cours..- 65 réponses
-
- 1
-
-
- imprimante 3d
- projet
-
(et 1 en plus)
Étiqueté avec :
-
Etude pour fabriquer une imprimante 3D à commercialiser
Vicaeman en réponse au topic de Vicaeman dans Projets et impressions 3D
Salut, merci pour la suggestion. J'y penserai quand je "cartériserai" le caisson. Bonjour, merci pour ta réponse à l'étude ! Tout à fait, les conseils qui proviennent de l'expérience personnelle me permettront de réaliser cette imprimante au mieux. Je me suis d'ailleurs moi-même inspiré des problèmes que j'ai rencontrés mais il y en a pleins que j'ignore, d'où l'étude. A propos des axes X/Y entraînés par vis sans fin je n'ai pas mené de tests de performance dessus mis à part les impressions faites, mais ce que je peux en dire : Avantages : - plus facile à installer qu'une courroie - Très peu de bruit à moins de paramétrer de grandes accélérations et même comme ça le bruit est plutôt couvert (je partagerai une mesure du bruit pendant l'impression au sonomètre si tu le souhaites) - robuste et pas besoin de maintenance type tension de courroie à faire donc pratique sur ce point - au niveau du mouvement, très précis, avec couplage du moteur et de la vis avec un accoupleur flexible (accoupleur à mâchoire pas testé) Inconvénients: - Plus cher qu'un système de courroie GT2 - il faut que le montage soit parfaitement aligné sinon lors de la rotation la vis se décale de son axe ce qui peut parasiter le mouvement du plateau ou de la tête (ça a été mon cas avec des pièces de structure pour le maintien de la vis que j'ai imprimées et qui avec la tolérance de la modélisation étaient pas parfaites comme les pièces usinées en alu.) - Difficile d'intervenir manuellement sur les axes par rapport au système à courroie lorsque les moteurs sont éteints. C'est faisable tout de même en tournant l'accoupleur à la main mais étant donné le grand rapport de réduction ça prend du temps pour faire 1 malheureux cm d'un autre côté ça témoigne justement d'une bonne précision. On ne peut pas tout avoir Finalement je préfère revenir sur un système de courroie pour la prochaine imprimante par soucis de simplicité de maintenance.- 65 réponses
-
- imprimante 3d
- projet
-
(et 1 en plus)
Étiqueté avec :
-
Etude pour fabriquer une imprimante 3D à commercialiser
Vicaeman en réponse au topic de Vicaeman dans Projets et impressions 3D
Oui, exactement, l'utilisation des profilés 2040 ou 4040 est intéressante pour ce genre de fixation avec des joints de calage. Le problème c'est que le joint à une certaine épaisseur qui fait que sur la fente de 6 mm, on ne peut pas mettre un panneau épais du coup c'est un peu plus fragile et souple sur les parois que si on fixait les panneaux avec des vis sur l'extérieur du cadre de l'imprimante.- 65 réponses
-
- imprimante 3d
- projet
-
(et 1 en plus)
Étiqueté avec :
-
Etude pour fabriquer une imprimante 3D à commercialiser
Vicaeman en réponse au topic de Vicaeman dans Projets et impressions 3D
Ah oui c'est vrai je connaissais pas très intéressant l'impression 3D non planaire, ça donne envie de tester. Pas de soucis je vous ferai part de l'avancement du projet au fur et à mesure. Salut, si en effet il y avait du balan mais pas lors de l'impression, plutôt si bon le bougeait à la main. J'ai ajouté deux plaques de fixation comme celles-ci : Plaque de fixation pour corriger et rigidifier et maintenant ça bouge plus. Il existe beaucoup de moyens de fixer le portique Z sur systéal. C'est un peu ma référence pour tout ce qui est structurel et je la conseille. Les profils 20x40 sont de type V oui. On en trouve justement chez systéal, jusqu'à 4.180 m. Tu peux aussi poser ton imprimante sur un tapis anti-vibration comme on peut utiliser pour une machine à laver, ça doit faire l'affaire pour absorber les vibrations. A tester... Ou bien fixer des paulsta mécanique comme ici : paulsta mécanique, c'est des composants mécaniques faits de caoutchouc, qui absorbent les vibrations comme des Damper pour moteur nema . C'est vrai, déployer l'imprimante de manière ludique est aussi une bonne idée. Oui c'est vrai en vissant on peut l'abîmer. Personnellement j'ai toujours vissé à la main pour contrôler le couple de serrage. Quel autre option me suggères-tu plutôt, du verre ? Merci pour la suggestion à propos des roulements, je vais me renseigner là-dessus.- 65 réponses
-
- 1
-
-
- imprimante 3d
- projet
-
(et 1 en plus)
Étiqueté avec :
-
Etude pour fabriquer une imprimante 3D à commercialiser
Vicaeman en réponse au topic de Vicaeman dans Projets et impressions 3D
Oui je vois, tu parles d'une déformation non homogène sur toute la surface du plateau. Mais qu'en est-il si le "coussin chauffant" fait la même taille que le plateau (310 x 310 mm). Ne devrait-il pas chauffer pareil toute la surface. Tout dépend de sa forme, mais en admettant que la répartition de la résistance chauffante dans le coussin soit régulière comme ici : on devrait avoir globalement la même déformation sur la surface et aux coins. En effet, la fiabilité des composants à température ambiante élevée comme ça peut être le cas dans un caisson où on imprime de l'ABS peut poser problème. Le MPU6050 et la raspberry peuvent fonctionner jusqu'à 85°C. Le LM2596 jusqu'à 125°C et et le servo-moteur jusqu'à 50 °C. J'ai sélectionnés ceux-là pour l'instant mais ils seront très probablement à redimensionner. notamment le servo, 50 °C de température c'est faible. Après comme je l'ai dis la manip de l'autoleveling peut ne se faire qu'une seule fois au démarrage à froid( c'est pas hyper logique c'est vrai) et sauvegarder la config peut importe la déformation à chaud puisqu'elle serait homogène. Salut, merci pour la suggestion. Waouu ! un composante issu du domaine spatial dans mon imprimante.. ça c'est vendeur Sinon, peut-être plus simple et moins cher, on peut augmenter l'épaisseur de la plaque en alu. Ca risque d'alourdir un peut l'axe Z mais honnêtement j'ai trouvé des moteurs nema 17 avec un couple élevé ici Nema 17, je pense qu'avec 2 y aurait pas trop de soucis. Merci pour ton commentaire, C'est une bonne question, à laquelle je ne peux pas encore répondre précisément. Pour l'instant je pencherais plutôt sur des grosses entités type entreprises, fablabs, universités plutôt que des particuliers. Mais, si le prix final est accessible, je pourrais peut-être élargir la clientèle. Du coup, pour une utilisation professionnelle, on veut pas avoir à bidouiller mais que ça fonctionne, que ce soit fiable et qu'il y est un SAV derrière j'en suis conscient, c'est pourquoi j'essaie de faire un système automatisé un maximum. Salut à toi, je me suis aventuré par curiosité sur ton site. Ayant lu la bio, je m'y suis aussi pas mal retrouvé par rapport aux loisirs et passions que tu mentionnent(l'astronomie, la musique, l'électronique ..) . J'ai commencé petit à bricoler avec un grand père qui m'a transmis la passion de l'électronique et de l'aéromodélisme. Assemblé mon premier pc fixe, démonté des voitures RC et autres appareils ménagers ect. fabriquer des avions RC. Je pense ne pas me tromper si je dis que beaucoup ici on commencé de la même façon en bidouillant dans un garage ou dans une chambre et continuent encore aujourd'hui.. Pour ma part, internet est né bien avant moi et était déjà bien fourni en sites et images (et pubs) lorsque j'avais besoin de renseignement. Je suis d'accord avec toi, il est vrai qu'aujourd'hui, se lancer seul dans un projet comme celui-ci c'est long, compliqué, et peut-être voué à l'échec. Mais comme tu le dis, je vais faire l'imprimante pour moi dans un premier temps, un prototype, fonctionnel, l'améliorer au mieux et après je verrai. Je suis des études en parallèle et c'est vrai que ça peut être compliqué de trouver le temps pour. Mais je travaille au moins 4h/jours sur ce projet, 4h que je ne vois pas passer d'ailleurs puisque c'est une passion. Petit à petit ça avance, et avec une bonne détermination on peut aller au bout et quand bien même ça prend pas sur le marché tanpis on apprend des choses et on fait mieux la prochaine fois. De plus, mes études me permettent d'avoir un suivi sur ce projet, et potentiellement un financement.- 65 réponses
-
- 1
-
-
- imprimante 3d
- projet
-
(et 1 en plus)
Étiqueté avec :
-
Etude pour fabriquer une imprimante 3D à commercialiser
Vicaeman en réponse au topic de Vicaeman dans Projets et impressions 3D
Bonjour merci pour ton retour, Oui oui j'ai déjà utilisé ce type de capteur et eu recours au nivellement automatique (semi-automatique du coup puisque le réglage du plateau se fait manuellement). On peut choisir 4,5 ou plus (ou moins) de points pour mesurer l'écart buse - plateau. Mais, si la structure mécanique est robuste, sans jeu et d'équerre, le plateau devrait être plat en tout point donc la buse devrait être à même hauteur partout. Si ce n'est pas le cas, et par rapport à ce que je présente, redresser le plateau en 1 ou plusieurs des 4 coins devrait permettre de corriger la planéité et ainsi que la buse soit à la bonne et même hauteur aux 4 coins et donc partout. Il n'y aurait donc pas besoin d'un BLtouch pour mesurer ça. Ensuite, pour ce qui est de la précision je suis d'accord avec toi les MPU6050 sont peut-être pas les plus précis mais la question est : est-ce que pour cette utilisation ils sont suffisants ou non ?. Le but c'est qu'ils détectent la plus petite variation de position par rapport à 0 qui doit être ensuite corrigée. Théoriquement, pas moyen de savoir, il faut tester.. De même pour les servos. Bonjour, merci pour ton retour également. Le polycarbonate est très résistant pour en avoir utilisé, 3mm je ne sais pas mais 5 mm, il est pratiquement impossible à casser. Je mets ici ces caractéristiques : - Bonne résistance à la chaleur - Pliage à froid - Excellente résistance au chocs, 250 fois plus résistant que le verre - Supporte des écarts de température importants : plage d'utilisation de -100°C à +120°C - Facile à transformer: se découpe, se plit, se visse - Protection de machines - Vitrage de sécurité etc. Ca me semble parfaitement adapté à cette utilisation. Après pour l'isolation thermique du caisson à voir. Tu as raison pour la rigidité, il faut que je me débrouille bien pour avoir le moins de jeu possible et un système robuste cela va de soit. PS : Aucun de vous ne me dit rien sur la fixation magnétique du plateau avec des aimants néodymes adhésifs de 1Kg pour moi c'est ce qui m'inquiète le plus car le plateau pourrait carrément se déplacer s'il est pas assez fixe. Je pense utiliser la plaque autocollante magnétique sous le PEI pour fixer le plateau en Alu anodisé (donc pas "aimantable") sur les supports à magnets.- 65 réponses
-
- imprimante 3d
- projet
-
(et 1 en plus)
Étiqueté avec :
-
Etude pour fabriquer une imprimante 3D à commercialiser
Vicaeman en réponse au topic de Vicaeman dans Projets et impressions 3D
Salut, merci pour ton retour d'expérience. Là si je pars sur une CoreXY ça devrait être plus simple de l'enfermer avec des panneaux. Je pensais utiliser des panneaux de polycarbonate qu'on peut trouver pour une épaisseur de 3 ou 5 mm (5 préférable pour la rigidité) chez Systéal par ex : Plaques PC. Je me demande encore si j'utiliserai des joints de calage pour insérer le panneau dans les rainures des profilés comme ici : joint de calage ou fixer sur l'extérieur avec vis/écrou M5. Aussi pour réguler la température à l'intérieur je pense utiliser un ventilateur d'aération combiné à une sonde de température type PT100 sur une raspberrry ou arduino. Auriez-vous d'autres systèmes à me suggérer ? Petite mise à jour : Plateau à nivellement automatique Je suis en train de travailler sur un système de nivellement automatique du plateau. L'objectif c'est de ne jamais avoir à faire de nivellement manuellement en serrant des écrous. Grâce à une fixation magnétique du plateau sur 4 supports articulés, 4 capteurs gyroscopiques 3 axes MPU-6050, 4 servos-moteurs SG90 une raspberry pi pico et un convertisseur de tension LM2596, on pourrait gérer automatiquement la planéité du plateau. La manip serait faite au démarrage de l'imprimante et/ou entre chaque hauteurs de couche ou encore en temps réel pendant l'impression (en fonction de la précision). Voilà la structure du plateau : et l'équipement: L'idée c'est d'utiliser l'alimentation de l'imprimante, une LRS350W de chez MeanWell de 24 V. Passer dans le convertisseur LM2596 pour abaisser la tension à 5V pour que le reste de l'équipement puisse fonctionner. En sortie du convertisseur on alimente la raspberry. On branche les 4 capteurs MPU à la raspberry pour récupérer les données de position du plateau aux 4 coins par rapport à la position de offset 0°. La raspberry contrôlera les 4 servos-moteurs en rotation en fonction des valeurs mesurées. Voilà à peu près ce que je souhaite faire: Pour rappel le plateau est fixé par 4 aimants neodyme de 1 kg comme ici : Aimant neodyme , cela permettra de le manipuler plus facilement, pas de vis et d'écrous. Du coup, voici quelques avantages à ce système : Avantages : Pas besoin de capteur type BLTouch, inductif ou autre Tête d’impression plus légère Possibilité d’imprimer plus vite (moins d’inertie) Correction en temps réel du plateau (optionnel et risqué, à vérifier lors du prototypage) Pas besoin de faire G29, Maillage Gain de temps, l’impression peut démarrer directement Pas d’écrous de nivellement et ressorts (plateau et axe Z plus léger) Si l’impression est plus lourde d’un côté (plus de matière) on va corriger la planéité, pour avoir une hauteur d’impression toujours cohérente. Invonénients : Utilisation de 4 capteurs, 4 servos, une carte de contrôle Probablement plus cher (à vérifier) Dites-moi ce que vous en pensez, ce que je pourrais améliorer ou changer etc.- 65 réponses
-
- imprimante 3d
- projet
-
(et 1 en plus)
Étiqueté avec :
-
Etude pour fabriquer une imprimante 3D à commercialiser
Vicaeman en réponse au topic de Vicaeman dans Projets et impressions 3D
Il me reste 1 ans et demi sur les 3. Merci pour les suggestions, howtomecatronics en effet une très bonne chaîne j'avais déjà vu quelques vidéos mais Dan Gelbart je connaissais pas. En voici quelques unes qui me viennent en tête aussi, personnellement je les trouves inspirantes: JLaserVideo, HackSmith, Plasma channel, Melkano, DIY Perks Ah oui je vois. Bon ça tombe bien, on m'a conseillé de faire une CoreXY fermée et pour réduire l'encombrement et pour pouvoir imprimer ces matériaux techniques. Je suis donc reparti là-dessus sur la conception.. Pas facile à mettre en place le système de courroie au premier abord, mais finalement une fois qu'on a saisit le truc ça va.- 65 réponses
-
- imprimante 3d
- projet
-
(et 1 en plus)
Étiqueté avec :
-
Etude pour fabriquer une imprimante 3D à commercialiser
Vicaeman en réponse au topic de Vicaeman dans Projets et impressions 3D
Salut, merci pour ton commentaire et l'abonnement et l'étude. Tu as tout à fait raison, le fait de faire évoluer le projet ça en apprend beaucoup tout au long. C'est vrai que le marché français est plus atteignable pour commencer. Justement, il y a quelques entreprises dans ma zone qui pourraient je pense être intéressées et quelques fablabs et fabriques d'impressions 3D qui potentiellement pourraient vouloir augmenter leur productivité (je vais me renseigner comme il faut là-dessus..) Ce n'est pas tout, l'imprimante 3D, j'ai comme un "Plan B" si on peut appeler ça comme ça, qui consiste à avoir une ferme de mes imprimantes et faire de la prestation de service d'impression en ligne. C'est la suite logique du projet si on veut. Qui plus est, ça renforce le fait de vouloir avoir des imprimantes qualitatives. Merci pour tes sages conseils. Je suis dans l'ingénierie Mécatronique en parallèle, c'est la roue de secours Salut, "Inutilisable avec des matériaux techniques" ? La tête d'impression vient de chez Slice Engineering. Il sont plutôt réputés pour faire de la qualité autant que E3D. Avec une buse en acier trempé on est assez peu limité je pense (qui peu le plus peu le moins). Référence de la tête :https://www.sliceengineering.com/products/copperhead-hotends . Tout dépend du secteur professionnel intéressé. Pour du prototypage, PLA, ABS, ASA, CARBONE, PETG.. tout est faisable. Je veux bien un exemple de matériau technique qui serait compliqué à imprimer sur ce genre de tête. Le SAV, en espérant ne pas avoir à en faire de trop gagnera en notoriété avec le temps et par la qualité du service au client. Une imprimante bien travaillée, fonctionne bien et n'a pas besoin d'être retournée (tous produit en général): c'est l'objectif, après on est jamais à l'abri. Après tout le reste se monte au fur et à mesure. Tout à fait d'accord ! Honnêtement je ne sais pas encore précisément qui seront mes clients( à définir avec l'étude). Pour de la vente plutôt au particulier, cela va dépendre de la budgétisation finale de l'imprimante et donc de ça conception. Si c'est trop élevé au final, faudra que je me restreigne aux entreprises. Après c'est pas les secteurs qui manquent, l'avantage c'est que y en a plusieurs qui pourraient en avoir besoin pour du prototypage rapide. Il faut juste les dénicher Salut, merci pour ton commentaire également. Je comprends totalement ce que tu veux dire. C'est justement pour cela que j'ai le second plan de fabriquer quand même des imprimantes pour constituer une ferme et faire de l'impression 3D, comme service de prestation. Comme ça si la vente venait à ne pas fonctionner il y aurait au moins cette alternative et au pire des cas, eh beh j'aurais pleins d'imprimantes pour augmenter ma productivité sur de futurs projets. C'est pas top ça ! Si vraiment rien de tout ça ne fonctionne, bon bah je me rangerais comme tout le monde, c'est pas un mal, j'aurais essayé et j'aurais forcément appris. Le dernier point que tu as soulevé est une grande question justement. J'avais dans l'idée de rendre l'imprimante "open source" et faire un kit en partageant comme tu dis les fichiers STL et les composants (et la conception va dans ce sens pour l'instant en montant un dossier de fabrication en parallèle) comme ça la structure étant personnalisable, ceux qui veulent auront accès gratuitement au fichiers. Je dis gratuitement, car je pense qu'il y a moins de personnes intéressées par le bricolage de leur imprimantes que des personnes qui veulent recevoir leur imprimantes toute faite et n'avoir qu'à démarrer en 3 clics. Je ne sais pas encore réellement pour ce point mais je pars sur l'idée de l'open source au cas où. Ceux qui aiment le DIY pourront la fabriquer de 0. Les autres devront acheter l'imprimante tout faite.- 65 réponses
-
- imprimante 3d
- projet
-
(et 1 en plus)
Étiqueté avec :
-
Etude pour fabriquer une imprimante 3D à commercialiser
Vicaeman en réponse au topic de Vicaeman dans Projets et impressions 3D
Bonjour à toi, merci pour ton commentaire. C'est vrai pour 1000 € ou moins tu peux trouver des imprimantes bien équipées, qui impriment très bien et qui font largement l'affaire. D'ailleurs pour seulement 200-300 € j'ai pu avoir une Wanhao D12-230 Pro qui faisait très bien le travail pour le rapport qualité/prix. La différence à mon avis entre un fabricant bien installé qui dispose d'un service de production industrialisé, un SAV et une communauté et "un gas tout seul" c'est bien sur la notoriété d'une part. En débutant, on est personne sur le marché, mais bon tout le monde à bien du commencer quelque part (et je monterai une équipe aussi plus tard). C'est à mon avis la qualité du produit qui fera qu'on se démarque ou pas. Ca tombe bien c'est là-dessus que je compte mettre l'accent. Or, qui dit qualité dit composant chers. Donc la facture monte. Maintenant, la différence entre un procédé de fabrication industriel et un procédé plus "artisanal" basé sur une expérience utilisateur c'est le côté personnalisation individuel qui change. Par exemple, tu ne peux pas faire évoluer la structure d'une Bambu Lab à ton goût si tu le souhaite, là où une imprimante faite de profilés modulaires tu peux (fixer une boîte pour ranger des outils d'impression, etc.) Aussi, je pense que les imprimantes sont de plus en plus complexes dans la fabrication et l'utilisation pour 'simplifier l'expérience utilisateur'. On a des firmware à mettre à jour pour garantir un bon fonctionnement, de l'automatisation des chauffes, du nivellement du plateau, maintient de température ambiante, tension de courroie semi-auto etc. (et il faut attendre que tout ça se fasse avant de pouvoir commencer) Est-ce qu'il ne faut pas revenir aux 'bases' avec des choses simples qu'un novice comme un professionnel peuvent utiliser (c'est à dire optionné, mais simple d'utilisation). Je reçois une imprimante, je branche la prise, j'allume, je mets une clé avec mon fichier ou par wifi, bouton démarrer et hop rien d'autre à faire. C'est ce que j'aimerais proposer, une imprimante qui puisse tout faire (sauf le café), pour tout le monde à un prix abordable aux amateurs mais pas de mauvaise facture pour les professionnels. Je suis convaincu qu'un produit complexe qui est simple parle mieux à tout le monde. SI je vois au démarrage qu'il faut déjà paramétrer 1000 choses avant de commencer ç'est déroutant. Je ne prétends pas pouvoir révolutionner l'impression 3D à l'internationale, tout existe déjà. J'aimerais juste présenter un n-ième modèle qui j'espère sera quand même attrayant de par sa simplicité. Après je suis conscient que c'est compliqué de satisfaire tout le monde et qu'il faudrait cibler. Mais j'ai envie d'essayer. On verra ce que ça donne. Bonjour, merci pour ton commentaire et ton encouragement. Pour les pièces tu n'as pas tord il y a des choses qu'on ne peut trouver que chez des revendeurs chinois (surtout l'électronique) mais je vais m'efforcer de privilégier un maximum des composants Made in France.- 65 réponses
-
- imprimante 3d
- projet
-
(et 1 en plus)
Étiqueté avec :
-
Etude pour fabriquer une imprimante 3D à commercialiser
Vicaeman en réponse au topic de Vicaeman dans Projets et impressions 3D
Salut à toi ! Merci pour ton commentaire et pour avoir répondu à l'étude. A propos des pièces, je pense plutôt essayer de me fournir un maximum en France, cocorico ! (quoique si ce n'est pas la livraison qui coûte chère, ce sera le prix donc question renta ...) c'est plutôt la qualité qui m'importe C'est vrai que la conception peut prendre du temps, mais quand on s'y prend bien ça peut aller vite. Il y a déjà beaucoup de pièces modélisées par exemple sur des sites comme Grabcad, qu'on peut récupéré et juste adapter (pourquoi réinventer la roue si elle existe déjà ) Par curiosité, si ce n'est pas indiscret, pourquoi les marges dans la vente de tes GPS on diminuées, à cause d'une concurrence montante et des prix concurrentiels ou à cause des taxes ou autre ? L'idée justement est de sélectionner le meilleur en terme de composant (en optimisant les coûts) afin d'éviter d'avoir un SAV trop important. Je compte me lancer aussi en autoentrepreneur pour commencer. Cela m'intéresserait d'avoir ton retour d'expérience là-dessus si tu acceptes que nous en discutions par mail en MP. Comment passer de petit à gros sans mettre les pieds dans l'entre-deux ?- 65 réponses
-
- imprimante 3d
- projet
-
(et 1 en plus)
Étiqueté avec :
-
Etude pour fabriquer une imprimante 3D à commercialiser
Vicaeman en réponse au topic de Vicaeman dans Projets et impressions 3D
Bonjour à toi, merci pour ton commentaire et tes suggestions. Oui en effet, je reste conscient qu'il faudra une marge sur le prix de vente, l'inverse serait impensable. Je garde bien en tête les aspects de l'entreprise dans ce type de projet notamment sur le fait d'avoir des composants "génériques" pour une modification, réparation, un Service de support client, la facilité et rapidité de prise en main et tout ce qui va avec le fait d'entreprendre. Merci pour ces liens très intéressants. C'est vrai que c'est un projet de longue haleine, mais j'ai besoin de savoir à quoi va ressembler le produit avant de me lancer dans toute la partie "administrative et gestion" (ça ne saurait tarder). D'ailleurs, je vous remercie tous pour vos remarques ici, qui sont toutes constructives et me permettent de revoir et d'avancer certains points tant dans la conception que l'étude du projet. PS : Je vous tiendrais au courant sur ce fil, de la mise à jour et de l'avancée.- 65 réponses
-
- imprimante 3d
- projet
-
(et 1 en plus)
Étiqueté avec :
-
Etude pour fabriquer une imprimante 3D à commercialiser
Vicaeman en réponse au topic de Vicaeman dans Projets et impressions 3D
Je vais justement repasser sur du guidage courroie pour pouvoir déplacer plateau et tête hors tension, c'est plus pratique que les vis notamment lorsqu'on a besoin d'accéder ai circuit dans la base de l'imprimante. aaahh.. en effet, je me suis bien trituré l'esprit à essayer d'optimiser la taille de la base pour qu'elle ne prenne pas trop de place et qu'on puisse poser l'imprimante dans pleins d'endroits. Le problème avec un plateau de 310 par 310 et si la tête doit aller d'un bout à l'autre ça implique de doubler la taille de la base. Par contre passer sur de la core XY implique de revoir une bonne partie de la conception... Merci à toi pour cette suggestion, je vais voir comment je peux résoudre ça. Oui c'est cela un Relais SSR j'ai raccourcis son nom. Et bien si je suis amené à imprimer du métal c'est peut-être mieux sur du verre. Je ne sais pas, je n'ai pas encore testé ça sur mon imprimante actuelle. 99 € la bobine de BASF de 1 Kg chez Makershop, faudrait que je trouve un échantillon Je vais passer sur une sonde PT1000 donc pas besoin d'amplificateur MAX31865 comme pour la PT100 et une précision de mesure de : +/- 0.3 + 0.002 °C ça devrait suffire. C'est que des nouveautés, du coup j'avance peut-être des choses fausses, il me faudra terminer le proto pour tester tout ça. Oui la conception en core XY paraît bien approprié en effet. Je vais devoir remanger de la 3D avant de pouvoir faire de la 3D Le système de guidage à l'air complexe, mais il m'en faudra plus pour m'arrêter je pense (j'espère) Eh bien ici, je conçois l'imprimante de zéro. Ce n'est pas des composants préassemblés où il n'y plus qu'a brancher. Je sélectionne vraiment tout. Cela fait un certain temps que je travaille sur ce projet et je suis bien déterminé à le concrétiser. Au niveau du coût, j'essaie vraiment d'optimiser pour avoir un rapport qualité/prix très correcte (en imprimant certaines pièces (en ABS donc si j'ai bien compris plutôt qu'en PLA)) par exemple. Ayant pratiquement terminé la conception pour le moment et avant les futures améliorations j'estime un coût de fabrication ne dépassant pas les 800 € ce qui est déjà très onéreux je l'avoue mais avec toutes les options discutées auparavant cela me paraît assez cohérent.- 65 réponses
-
- imprimante 3d
- projet
-
(et 1 en plus)
Étiqueté avec :