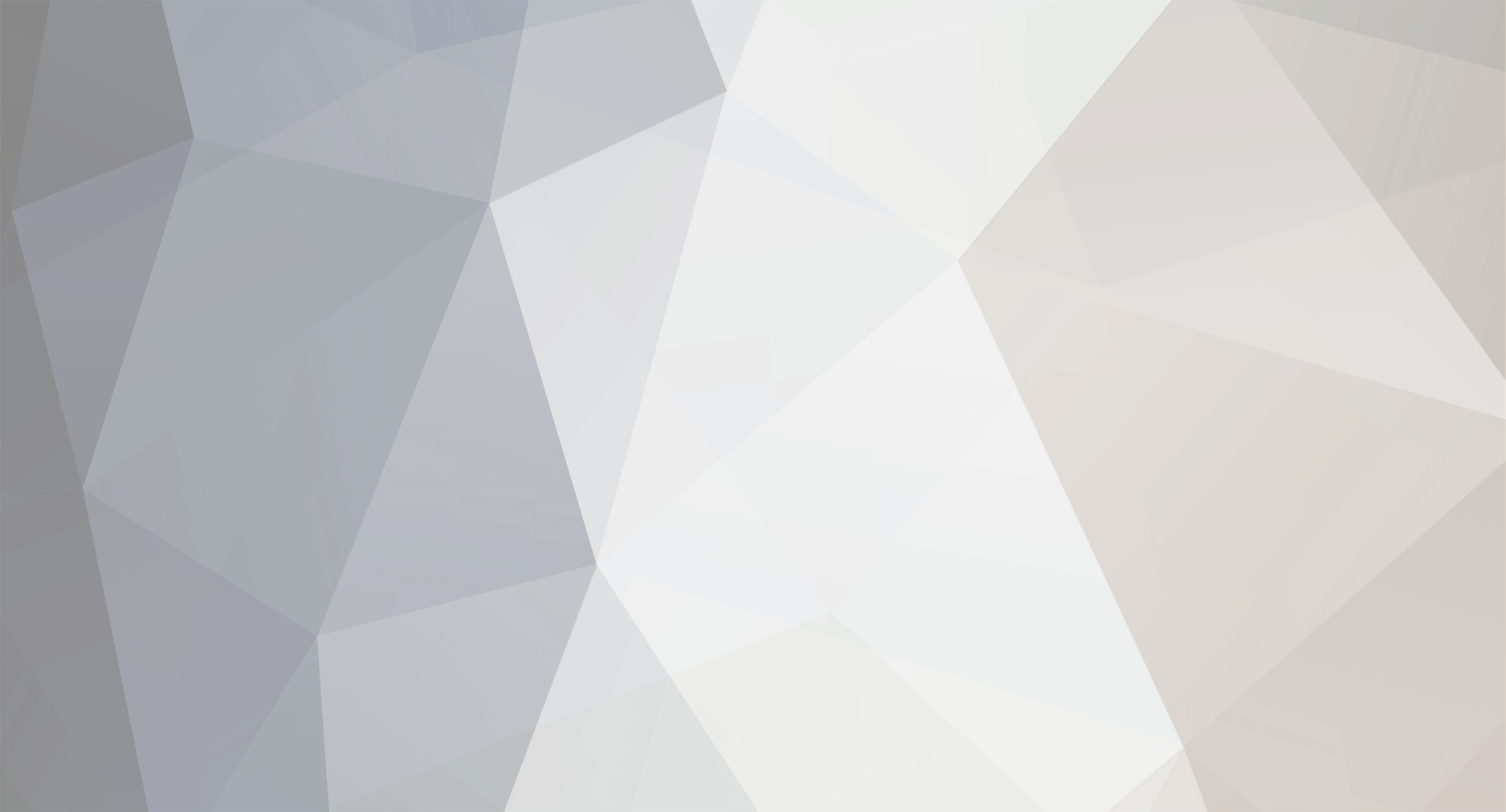
mdelanno
Membres-
Compteur de contenus
22 -
Inscrit(e) le
-
Dernière visite
Tout ce qui a été posté par mdelanno
-
J'ai exactement le même bruit mais je n'avais pas pensé aux roulements. Si tu arrives à le reproduire en bougeant à la main le chariot, je pense que tu dois les démonter, puis les glisser un par un sur une tige et les faire coulisser pour identifier ceux qui sont défectueux. Tu peux aussi inspecter visuellement ou en passant ton doigt tes tiges de guidage pour voir s'il n'y a pas de sillons. Il y a des vidéos avec des bruits un peu similaires ici : https://ultimaker.com/en/community/9649-hbk-linear-bearings-clicking et là : Mais je crois que tu n'en auras le cœur net qu'en démontant tout et en remplaçant les roulements...
-
D'après cette discussion, on dirait que les buses E3D sont compatibles avec l'Hexagon. Elles sont toutes les deux en M6. Tu peux télécharger le plan de l'Hexagon ici : http://download.lulzbot.com/TAZ/accessories/hot_ends/Hexagon_v2_Hot_End/lulzbot_edition_hexagon_hotend-0.5mm/brass_nozzle_3mm-0.50mm_v0.2.PDF et le plan de l'E3D V6 ici : https://wiki.e3d-online.com/images/3/3a/V6-NOZZLE-ALL.pdf
- 30 réponses
-
- emotiontech
- microdelta rework
-
(et 2 en plus)
Étiqueté avec :
-
Ta pièce doit passer car si le rayon d'impression conseillé est de 55 mm, on peut pousser à 60. Sinon avec un raft tu dois pouvoir l'imprimer verticalement. Pour ce qui est des pièces en acrylique, je n'ai pas de problème avec les miennes. Il faut simplement faire attention à ne pas serrer trop au montage (et il y a le film à retirer sur chaque pièce, c'est assez pénible). Dans le pire des cas, tu peux imprimer des pièces de remplacement, il y a par exemple magic_mushrooms qui a remodélisé toutes les pièces : http://www.thingiverse.com/thing:1039441
-
J'avais le même problème sur mon imprimante (qui n'est pas une Discovery). Dès que je faisait une impression de plus de deux heures, une fois sur 2, elle s'arrêtait en plein milieu. Je pensais que ça venait du câble USB ou de l'ordinateur, j'ai donc investi dans un LCD + lecteur de carte SD. Deux impressions plus tard, rebelote, arrêtée en plein milieu. C'était un problème avec la carte SD (j'avais une erreur du type Read Error affichée sur le LCD). J'ai changé la carte, plus de Read Error, mais elle s’arrêtait encore (j'en devenais dingue). Je me suis dis que c'était peut être des perturbations électriques qui faisait planter la carte. J'ai installé 4 anneaux de ferrite sur les départs des câbles des moteurs et jusqu'ici je n'ai plus de problème, mais c'est peut être une coincidence. En tous cas ça vaut la peine d'essayer, ça coûte 1 € l'anneau (chez Conrad donc on doit pouvoir trouver moins cher). On peut aussi en récupérer dans certains équipements électroniques (j'en ai trouvé un par exemple dans un vieux lecteur de DVD). J'ai vu qu'il y en avait dans les Ultimaker et dans les Lulzbot, donc je suppose que ça a une utilité. Sinon tu peux vérifier les points suivants : Si c'est un problème dans le fichier, si tu relances l'impression, ça doit s'arrêter exactement au même endroit ; Ca peut être un problème de composant qui chauffe. Dans ce cas, il faut que tu surveilles l'impression et quand elle s'arrête, vérifier la température des composants. Ou alors installer un ventilateur ; Ca peut être une micro coupure de courant. Si tu as un onduleur, il faudrait essayer de brancher ton imprimante dessus. Mais normalement avec une Discovery je pense que dans ce cas de figure que l'impression aurait du redémarrer ; Ca peut être un problème au niveau d'un fin de course. Le firmware peut être configuré pour surveiller en permanence les fins de course et je pense que s'il détecte un signal il doit arrêter la machine pour raison de sécurité (tu peux tester si c'est le cas sur ta machine en lançant une impression et en enfonçant un des capteurs). Sur Repetier-firmware, la variable c'est ALWAYS_CHECK_ENDSTOPS (je ne sais pas quel est le firmware installé sur une Discovery). Il parait que si un de tes cables moteurs est proche du câble d'un fin de course, il peut y avoir un courant induit qui provoque un faux signal. Ou alors ton capteur est défectueux.
-
Non parce que le fil qui est déposé vient se coller aux couches déjà imprimées. Je ne pense pas que la gravité aura un effet notable sur les couches intérieures. Par contre quand on imprime sur les bords et qu'on a un surplomb, à un moment donné ça va décrocher je pense :
-
Ce qui est intéressant avec la solution de @J-Max.fr, c'est que les ponts parallèles à l'axe Y vont être impeccables, puisque le filament va être déroulé verticalement (enfin le fil restera rond dans la partie non supportée alors qu'il est écrasé ailleurs). Après pour les surplombs et les supports, je ne sais pas trop ce que ça peut donner. Je pense que ça peut marcher car les nouvelles couches vont s'accrocher aux précédentes, mais j'ai peur qu'il y ait une différence visible entre le bas et le haut (enfin l'avant et l'arrière de la pièce, on est perdus avec cette disposition inhabituelle). Peut être même que les supports deviendraient inutiles. En fait il faudrait que le plateau tourne autour de l'axe horizontal et que la tête ne bouge pas en X, comme ça le fil serait toujours déroulé suivant l'axe vertical et il s'affranchirait donc de la pesanteur, comme dans l'ISS. Il faudrait donc passer en coordonnées cylindriques.
-
La notation scientifique je n'aime pas trop car on a vite fait de se tromper. C'est comme les conversions d'unités, on a vite fait d'oublier ou de mettre un zéro en trop. Je vois pas trop ce que tu veux dire, mais c'est vrai qu'avec des roues je pense que le coefficient de frottement/de roulement peut varier dans de fortes proportions car normalement on règle le jeu avec des excentriques et si le gars qui fait le montage sert trop fort, ça peut engendrer des efforts plus importants que prévu. Donc effectivement, je pense qu'il faut prévoir plus large avec ce type de liaison. Il faut que je regarde ça à tête reposé pour être sûr, mais je pense que comme tu es vertical, le poids travaille dans le sens de la courroie et donc tu dois l'ajouter aux efforts. Je referais la note de calcul à la main quand j'aurai un peu de temps. Je pense que je pourrai aussi prochainement tester le levage de 500 g avec un moteur de 50 N.cm. Pour ce qui est de la pièce couchée, son poids va avoir tendance à la décoller du support. Ca peut être problématique, surtout si on utilise du scotch pour augmenter l'accroche, car ce dernier au bout de quelques impressions a tendance à se décrocher. Mais bon il faut tester, c'est difficile à apprécier sans avoir fait des essais.
-
@J-Max.fr Sauf erreur de ma part et si je suis bien réveillé, 4,594e-2 N.m, ça fait 0,046 N.m, pas 0,46 N.m. C'est l'équivalent de 4,594 x 0,01. Sinon, tu as utilisé un diamètre primitif de poulie de 10 mm. Je suppose donc que tu comptes utiliser une poulie GT2 16 dents (Dp = nbreDents x pas / PI). Est-ce que ce n'est pas gênant pour la résolution ? Parce qu'en pas entier, tu auras une résolution de 0,16 mm (160 µm) et les hauteurs de couche standard (0,1 par exemple) ne sont pas des multiples de cette valeur. Je pense qu'il faut utiliser une poulie de 20 dents à la place, ce qui va en pratique augmenter le diamètre (10,19 -> 12,73) et donc le couple requis. Tu devras aussi utiliser du microstepping et donc ça va réduire ton couple de 30% (Source). A première vue, le calculateur de Oriental Motor ne prend pas en compte ce paramètre. Pour le coefficient de frottement, si j'ai bien compris tu va utiliser des roues et donc j'aurai pris 0,005 au lieu de 0,5 puisqu'on va être en roulement. Bizarrement, la calculette ne permet pas de descendre en dessous de 0,01 (je ne comprends pas trop, ils pensent qu'on utilise des patins dans des applications de précision ?). Ca ne change rien pour l'axe Y puisqu'on est vertical, mais il faut en tenir compte pour l'axe Z. Ensuite, la masse que tu rentres dans la section Load and linear guide n'est prise en compte que pour le calcul de l'inertie, donc tu dois la reprendre dans External force pour l'axe Y. Enfin, je ne suis pas électricien et encore moins électronicien, mais les couples donnés par les constructeurs sont mesurés quand le moteur est alimenté avec 24 V et dans des conditions optimales. Comme je suppose que vous allez utiliser une alimentation 12 V avec une carte d'entrée de gamme, vous n'aurez pas le couple maximal annoncé. Sinon, coucher la machine c'est pas con, ça permet d'optimiser la structure.
-
Oui c'est vrai. J'avais prévu pour ça un rond diamètre 5 mm, deux roulements et deux poulies GT2 20 dents alésage de 5. C'est pas le bout du monde non plus.
-
Je viens de tomber là-dessus : https://www.thingiverse.com/thing:15132 (un concept de Johann Rocholl, qui est je crois l'inventeur de l'imprimante 3D delta). Combiné à des axes tournants comme sur l'UM, on peut peut-être en tirer quelque chose...
-
En fait, je suis en train d'explorer le concept de la delta inversée. Je participe à la discussion parce que c'est très intéressant, mais je ne pense pas réaliser à terme l'imprimante. Si je devais choisir, je partirais sur un mouvement de type C car je pense que c'est le plus simple. Il y a d'autres mouvements qui paraissent intéressants, surtout pour rendre la partie mobile plus légère, mais avec un chariot plus lourd on peut utiliser un entrainement direct au niveau de l'extrusion ou des têtes multiples, alors qu'avec un CoreXY ou HBot, c'est plus cohérent d'utiliser un Bowden. Et une longue courroie ne me plait pas trop, je ne sais pas si on peut la tendre correctement et d'après ce que j'ai lu, ce genre de système est compliqué à régler.
-
Et bien c'est le système Ultimaker. Avantages : Ensemble mobile léger car les moteurs sont fixes donc faible inertie, accélération plus rapide et moins de vibrations. Inconvénients : Plus d'axes, dont certains rotatifs donc besoin de 8 paliers ; Plus de courroies (4 au lieu de 3) et donc plus de poulies ; Certains chariots (les bleus et les verts dans ton dessin) coulissent sur des axes qui tournent, donc on ne peut pas utiliser de douilles à billes car ces dernières n'acceptent pas de mouvement de rotation ; Si tu disposes les moteurs en bout d'arbre, ils vont sortir de la cage. Donc tu est obligé d'ajouter des poulies et des courroies pour déporter les moteurs. En bref, tu privilégies la vitesse et la qualité au détriment du coût.
-
Pour avoir une partie mobile légère (sans moteur embarqué) sans avoir une courroie de 3 km de long et donc gagner en inertie, gagner en accélération et en vitesse.
-
Le robot 5 axes (sachant qu'à mon avis 4 suffiraient) est approprié si tu veux un volume de travail illimité comme par exemple ce projet de construction de pont : https://www.lesimprimantes3d.fr/robot-construction-pont-impression-3d-20150618/
-
C'est du polaire : Un pivot c'est bien plus simple qu'un mouvement linéaire : 2 roulements, un axe, deux poulies. C'est précis, pas cher et il n'y a pas plus rapide.
-
Je ne vois pas ce que ça change en terme de précision. Si le lit est en alu, ça ne pèsera pas tant que ça. La pièce en elle même ne pèse pas grand chose. Tu pourrais venir déposer des roulements dans la pièce en cours d'impression par exemple pour les noyer à l'intérieur. Bon ce serait délicat pour décoller la pièce car la structure ne pourrait pas encaisser beaucoup d'effort, mais on pourrait imaginer un système manuel de bridage du plateau. La machine serait énorme évidemment puisqu'elle devrait faire au moins 2 à 3 fois la taille du plateau, mais elle offrirait bien plus de possibilité qu'une imprimante classique. Elle pourrait assembler un objet complexe. Et la vitesse serait réduite mais on ne peut pas tout avoir. De toutes façons à partir d'une certaine vitesse l'extrudeur ne suit plus.
-
Disons que comme la tête est fixe, tu pourrais innover à ce niveau. Par exemple tu pourrais imaginer un barillet avec 6 têtes par exemple qui tournerait autour de l'axe vertical et qui permettrait de travailler avec 6 couleurs différentes. Ou alors 1 tête d'impression, 1 tête avec un foret, 1 tête avec une fraise, une tête qui distribuerait des écrous...
-
Pour la mobilité je dirais que je vois mal comment on pourrait faire bouger le lit et la pièce dans les 3 directions. Donc ça élimine A. Le D ça demande une tête légère donc on ne peut pas mettre un système d'entrainement direct et ça nous conduit tout droit vers une delta. Reste le B (CN), le C (Prusa) et le E (Ultimaker). Le B va conduire à une machine énorme puisque il faudra 2 fois la taille du lit en X et Y + une largeur de tête. Reste donc le C et le E, comme la quasi totalité des machines actuelles...
-
Effectivement, il y a bien une franchise de 150 euros sur les droits de douane, mais pas sur la TVA, qui représente le plus gros du montant. Bien évidemment, la douane n'a pas les moyens de contrôler tous les colis et donc la plupart des colis à destination des particuliers de petit montant passe sans difficulté la frontière, donc ce n'est pas un soucis pour vous. Le problème c'est que le calcul du couple est assez délicat car il peut varier suivant la qualité des pièces (qui peuvent varier énormément si c'est du pas cher), le montage (qui sera réalisé par chaque participant) et la lubrification. Donc même si tu veux le calculer précisément, ça ne sert à rien parce que tu devras prendre une marge de sécurité conséquente. Et au final la différence de coût entre un moteur puissant et un moins puissant n'est que de quelques euros. En plus c'est difficile de trouver les caractéristiques des moteurs, surtout leur couple dynamique. D'ailleurs sur le Wiki RepRap, ils se bornent à recommander un couple de maintien mini (44 N.cm). J'avais un stagiaire qui avait calculé ses moteurs pour un mécanisme. Quand il les a installé, son mécanisme n'a pas bougé d'un poil car il avait surestimé son rendement.
-
Les profilés aluminium à rainures 20x20 ne coûtent presque rien pour des longueurs de 300 à 400 m sur le site de Motedis (ailleurs il semblerait que ce soit beaucoup plus cher). Mais pour les assembler il te faudra obligatoirement des écrous spéciaux et c'est 22 € la pochette. Tu peux peut être utiliser des écrous H standard mais il faudra les meuler un par un. Ensuite il te faudra des vis d'une longueur précise car la rainure n'est évidemment pas profonde. Une pochette de 100 M4x8 c'est 14 €. Et suivant ce que tu veux fixer il te faudra du M3, du M4 ou du M5. Un vrai casse tête. Dans l'idéal, si tu ne veux pas jongler avec 140 outils, il faut du 6 pans creux. Il faut aussi ajouter des équerres et éventuellement des plaques de connection. L'alternative c'est d'acheter un kit de profilé. Il y a par exemple un portique pour une imprimante qui est vendu 89 € ici : http://3dmodularsystems.com/fr/accueil/131-kit-chassis-pour-imprimante-3d-scalar-xl.html et sur certains sites que je ne parviens pas à retrouver il y a des kits pour la robotique. Mais il faudrait certainement recouper les profilés et je ne suis pas sur de la méthode à employer pour avoir une coupe nette et précise. Si tu veux rester avec de l'aluminium, tu peux utiliser aussi des cornières aluminium comme sur la SmartCub3D. D'après la liste des pièces, ce sont des cornières épaisseur 1,5 comme celles qu'on trouve dans les grandes surfaces de bricolage. Mais il faut les couper et les percer précisément. Ensuite il faut imprimer tous les coins. Et je m'interroge sur la rigidité car 1,5 c'est léger. Le profil en lui même est assez résistant, mais l'aile fléchit facilement. Après tu peux utiliser du bois, des plaques de plastiques ou même souder des profilés acier. En fait ça dépend de l'outillage dont tu disposes. Personnellement je n'ai que de l'outillage electroportatif donc j'ai opté pour les profilés aluminium à rainures coupés à la longueur exacte. Je pourrai allez au FabLab le plus proche pour découper des plaques de bois ou autre, mais je dois faire 40 km, payer 90 € d'adhésion comme j'ai une entreprise + 40 € / heure pour utiliser une machine. Et je dois en plus ajouter la matière première. En résumé, le chassis, c'est ce qui fait la différence de prix. Tu peux faire une boite en contreplaqué pour quelques euros mais bon c'est pas très sexy, ou alors tu fais quelque chose de plus élaboré et ça te coûte plus cher. Pour les achats, je ne suis pas un spécialiste de la question, mais quand vous achetez sur des sites situés hors de l'UE, vous êtes censés payer les droits de douane, la TVA et peut être des frais de dossier pour le transporteur. Alors évidemment pour des faibles sommes et en tant que particulier, vous vous en fichez, mais je tiens quand même à vous le rappeler... Donc il s'agit de savoir si 300 € c'est HT (du genre je remplis mon caddy chez AliExpress) ou TTC (+ 20%, j'achète dans l'UE ou en respectant les contraintes légales).
-
Entre les deux mon coeur balance
mdelanno en réponse au topic de Phoenix dans Bien choisir son imprimante 3D
Une tige de diamètre 8 mm en acier de 350 mm de longueur ne fléchit pas de 0,1 mm sous son propre poids. C'est une poutre sur 2 appuis simple avec une charge répartie uniforme sur toute la longueur. La flèche maximale, située au milieu de la poutre, se calcule avec la formule suivante : f = -5qL^4/384EI q = charge. C'est le poids linéaire de la poutre. On a un diamètre de 0,008 m, donc la section c'est PI x r² = 3,1415 x 0,004² = 0,000005027 m². La densité de l'acier, c'est 7 850 kg/m^3. Donc 1 m de barre = 0,394 kg. En charge linéaire, ça nous donne 0,394 x 9,81 = 3,865 N/m ou 38,65 daN/m. Notre longueur de 350 mm pèse 138 g. L = longueur de la poutre, donc 0,35 m E = module d'élasticité longitudinale ou module de Young = 21 000 daN.mm^-2 pour de l'acier. I = Iz = moment quadratique de la section. Pour un rond c'est PI x d^4 / 64, donc 3,1415 x 0,8^4 / 64 = 0,02 cm^4 Notre flèche c'est donc -5 x 0,003865 N/mm x 350 mm ^4 / (384 x 210 000 N.mm^-2 x 200 mm^4) = -0,018 mm Il faut environ 400 g pour faire fléchir une tige lisse diamètre 8 de 0,1 mm. Comme les machines sont en général équipées de 2 tiges, du 8 suffit pour un chariot pas trop lourd (Bowden comme sur la discovery, qui doit faire moins de 500 g), sachant que la différence d'altitude entre le centre et le bord du plateau si on considère un surface de travail de 200 mm de large sera d'environ 0,04 mm (40 µm). Et suivant comment est construit la machine, on peut considérer qu'on est encastré aux 2 extrémités, donc ça diminue encore la flèche. Il faut aussi évidemment qu'il n'y ait pas trop d'effort dynamique induit, pour cela, il faut que l'attache de la courroie sur le chariot soit proche du plan des barres. Sur une Ultimaker, je crois qu'ils utilisent des barres diamètre 6 si j'en juge par rapport à la nomenclature. Sur une Prusa, il y a un moteur pour l'extrusion sur l'axe X. Ce moteur pèse à lui tout seul 330 à 350 g. Donc effectivement les tiges de 8 sont limites car le chariot doit approcher du kilo. Avec du diamètre 10, il faut un kilo par barre pour obtenir une flèche de 0,1 mm. Je pense que certaines imprimantes doivent avoir des barres qui ne sont pas droites car quand elles arrivent en longueur de 1 m par exemple, elles doivent être relativement facile à plier. Donc ça doit affecter la première couche. Les suivantes elles ont toutes le même profil donc ça ne doit pas être gênant, elles restent parallèles. Pour vérifier le dimensionnement de vos barres, vous pouvez utiliser des calculettes en ligne comme celle ci par exemple : http://jean.lamaison.free.fr/flexion.html -
300 € ça me semble irréaliste. Si quelqu'un prenait 2 heures pour établir une nomenclature du matériel nécessaire, il verrait que ces 300 € sont vite atteints : 4 moteurs avec un couple correct = 50 à 60 € 1 carte de contrôle = 30 à 50 € guidage = 50 à 70 € (douilles à billes + tiges rectifiées qui ne sont pas données) structure (profilés, équerres, plaques de jonctions, visserie) = 40 à 100 € (là dessus je ne suis sur de moi, je n'ai pas encore arrêté ma liste définitive) hot end = 50 € (je pense que c'est le composant le plus important donc je n’achèterai pas une copie). courroies, poulies, vis, coupleur... = 20 à 40 € visserie (c'est du petit diamètre <= M3, ça ne se trouve pas au Casto du coin, donc vous allez dépenser plus en frais de livraison que le coût réel des pièces) = 20 € alimentation = 50 € si vous voulez alimenter un grand plateau chauffant ventilateurs, fin de courses = 10 à 20 € pneufit, PTFE, MK8... Le kit Discovery 200 de Dagoma, c'est déjà une sacrée performance. Je ne pense pas qu'ils se gardent beaucoup de marge. L'économie principale c'est sur le guidage et la structure et je suis sur que cette dernière doit leur coûter plus cher que prévu parce que ça ne doit pas être de la tarte d'imprimer ces grosses pièces précisément de façon industrielle (Lulzbot le fait mais leurs machines sont bien plus chères). Peut être que vous pouvez baisser le prix en groupant vos achats, mais vous devrez être nombreux et ça ne se jouera que de quelques %. Après, vous pouvez toujours passez des heures à essayer de chercher à gagner quelques euros ici ou là, mais vous aurez des délais de livraison à rallonge et peut être pas toujours du matériel utilisable. Et bon, ça va allez à l'encontre de l'objectif qualité recherché. Soit vous visez une machine d'entrée de gamme pour permettre aux débutants de commencer l'impression 3D et donc là il faut conserver le budget de 300 €, soit vous voulez une machine fiable, précise et innovante et là je pense que c'est plutôt 700 à 800 €. Et à ce prix, votre imprimante ne sera ni mieux, ni pire que celles qu'on trouve sur le marché, puisque inévitablement vous allez utiliser les mêmes composants que les autres et les mêmes approches. La conception des imprimantes actuelles est le fruit de beaucoup de travail et les opportunités d'améliorations qui changent la donne sont plutôt rare. Il y a des imprimantes comme la Tiko qui regorgent d'innovations, mais je ne suis pas sur qu'elle tienne ses promesses, ni même qu'elles soient effectivement commercialisées un jour... Enfin bon, concevoir une imprimante ça reste très intéressant et très instructif, mais restez réalistes.